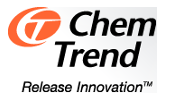
Ultrapurge
Purging Compound Introduction
There are two major classes of purging compounds in the market. One is referred to as mechanical or abrasive purging compounds. These are compounds where the cleaning process is based on the mechanical action of hard particles, e.g., glass fibers. The other type of purging compounds is chemical purging compounds. With these, the cleaning process relies on chemical additives that initiate some form of chemical reaction.
Abrasive purging compounds provide fast and reasonably effective cleaning, but they can also damage screws and cylinders/barrels. It is dangerous to use them in hot runner systems, through screen packs or melt pumps. Abrasive purging compounds are more difficult to evacuate from the machine, creating greater potential for longer-term damage as well as for production-run contamination and scrap creation.
Chemical purging compounds are safer for the equipment and may also be processed through screen packs and melt pumps. They are universally usable in hot runner systems and can be injected in cavities when a purge compound with an appropriately suitable MFI is selected. Because they are safer for the equipment, they are also more suitable for using as part of a preventative maintenance program as opposed to only as a “problem-solving product.”